How to Use CNC Programming to Improve Precision in Router Machines
To fully harness the potential of CNC programming in router machines, it's essential to follow best practices that ensure optimal performance.
CNC (Computer Numerical Control) programming is at the heart of modern manufacturing, providing enhanced precision, efficiency, and automation to a wide range of machining processes. Specifically, when it comes to router machines, which are essential tools in industries such as woodworking, plastics, and metalworking, CNC programming plays a crucial role in ensuring that intricate cuts and designs are executed with exact precision. By leveraging CNC programming, businesses can significantly improve the accuracy and consistency of their router machines, reducing human error and increasing production efficiency. This article will explore how CNC programming can be utilized to enhance the precision of router machines, discussing key aspects such as the basics of CNC programming, its impact on router machines, and best practices for implementation.
Understanding CNC Programming
At its core, CNC programming involves writing a set of instructions that control the movement and operation of a machine tool. These instructions are written using a programming language such as G-code, which dictates every aspect of the machine’s behavior, from speed to direction and depth of cut. For router machines, CNC programming is essential in creating complex, highly detailed cuts in materials like wood, composites, and metals. The accuracy of the final product largely depends on the quality of the CNC program and how well it is executed by the router machine.
Router machines, unlike manual machines, rely on precise, automated movements dictated by the CNC Programming and Router Machines. These machines operate by following a predefined path set out by the program, ensuring that cuts are repeated consistently with minimal variation. The key to improving precision through CNC programming is to carefully calibrate the machine, optimize the programming for specific materials, and make use of advanced features like tool compensation and multi-axis control. By understanding the full scope of CNC programming, manufacturers can harness the full potential of router machines to create high-quality, accurate products.
Improving Router Machine Precision with CNC Programming
One of the most significant benefits of using CNC programming in router machines is the drastic improvement in precision. Traditional manual methods often involved a lot of guesswork, physical adjustments, and reliance on the skill of the operator. In contrast, CNC programming eliminates most of these variables by relying on computerized systems that can execute exact movements based on predefined codes. This results in consistently accurate cuts, especially in high-volume production runs, where manual methods would struggle to maintain consistency.
CNC programming also allows for the use of complex geometric shapes and intricate designs that would be difficult or impossible to achieve manually. Router machines equipped with CNC technology can follow complex cutting paths with high precision, ensuring that each product is manufactured to the exact specifications. Additionally, advanced CNC programs can adjust parameters such as cutting speed, feed rate, and depth of cut to optimize performance for different materials, further enhancing precision. For industries where high tolerances and intricate designs are critical, CNC programming is an indispensable tool for achieving the desired level of accuracy.
Best Practices for CNC Programming in Router Machines
To fully harness the potential of CNC programming in router machines, it's essential to follow best practices that ensure optimal performance. One of the first steps is to carefully set up and calibrate the router machine. Proper machine calibration ensures that the toolhead, spindle, and other components are aligned correctly, preventing errors during operation. This includes checking the machine's zero points and ensuring that the workpiece is securely clamped in place. Without proper calibration, even the most precise CNC program will not produce the expected results.
Another best practice is to use tool compensation within the CNC program. Tool compensation allows for adjustments to be made in real-time to account for variations in tool diameter or wear. This ensures that the cutting tool maintains its correct position relative to the workpiece, preventing deviations that could affect the precision of the cuts. Additionally, it is important to simulate CNC programs before actual machining begins. Using simulation software can help identify potential issues with the program, such as collisions or incorrect tool paths, and allows for adjustments to be made before the router machine starts operating. This proactive approach can save time and reduce the risk of costly mistakes.
The Role of Technology in Enhancing CNC Programming for Router Machines
Advancements in technology have played a significant role in enhancing the capabilities of CNC programming, particularly for router machines. One such advancement is the introduction of advanced CAD (Computer-Aided Design) and CAM (Computer-Aided Manufacturing) software. These tools allow engineers and programmers to create highly detailed 3D models and translate them directly into CNC code, which is then used by router machines. CAD and CAM software streamline the entire design-to-production process, reducing the chances of errors and improving the overall quality of the final product.
Furthermore, the integration of multi-axis CNC programming has revolutionized router machine precision. Traditional router machines typically operated on a 2-axis or 3-axis system, meaning they could move along two or three directions. However, modern router machines can now be programmed to work with 5-axis or even 6-axis systems, allowing for greater flexibility and precision in complex geometries. Multi-axis systems enable router machines to access multiple sides of a workpiece in a single pass, reducing the need for re-positioning and further improving the precision of the cuts. By embracing these technological innovations, manufacturers can significantly enhance the performance of their CNC programs and router machines, achieving even higher levels of accuracy.
Overcoming Common CNC Programming Challenges in Router Machines
While CNC programming offers numerous advantages in terms of precision, it is not without its challenges. One common issue is ensuring that the CNC program is compatible with the specific router machine in use. Different router machines have varying capabilities and limitations, such as the number of axes they can operate on and the types of materials they can handle. Therefore, it's essential for CNC programmers to have a thorough understanding of the machine's specifications and capabilities to create effective programs that maximize its potential.
Another challenge is the need for ongoing maintenance and calibration of both the router machine and the CNC program. Over time, router machines may experience wear and tear, which can impact their precision. Additionally, as new tools are introduced or adjustments are made to the machine setup, the CNC program may require modifications to ensure continued accuracy. To overcome these challenges, it is important to establish regular maintenance schedules and continually update CNC programs as needed. By addressing these potential issues proactively, manufacturers can ensure that their CNC programs continue to deliver precise results over the long term.
Conclusion
CNC programming is a powerful tool for improving precision in router machines, offering numerous benefits that enhance the accuracy, consistency, and efficiency of the machining process. By understanding the basics of CNC programming, utilizing best practices, and embracing technological advancements, businesses can unlock the full potential of their router machines and achieve the highest levels of precision. Whether you are working in woodworking, metalworking, or any other industry that relies on router machines, incorporating CNC programming into your operations is essential for staying competitive and delivering high-quality products. Through proper setup, calibration, and ongoing refinement, CNC programming can help you achieve the precision necessary to meet the demands of modern manufacturing.
What's Your Reaction?

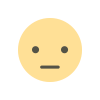




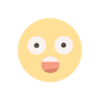